KBK智能起重機選型手冊:汽車零部件車間搬運效率提升策略解析
發布時間:
2025-02-24
在汽車零部件生產車間,物料搬運的效率直接關系到生產線的流暢性與成本控制。面對狹窄的空間布局、高頻次的零部件轉運需求以及精密裝配的精度要求,傳統起重機往往難以滿足靈活性和效率的雙重需求。而KBK起重機憑借模塊化設計、智能控制和高適應性,成為越來越多企業的首選。本文將從實際場景出發,為汽車零部件車間提供一套清晰的KBK智能起重機選型策略。
在汽車零部件生產車間,物料搬運的效率直接關系到生產線的流暢性與成本控制。面對狹窄的空間布局、高頻次的零部件轉運需求以及精密裝配的精度要求,傳統起重機往往難以滿足靈活性和效率的雙重需求。而KBK起重機憑借模塊化設計、智能控制和高適應性,成為越來越多企業的首選。本文將從實際場景出發,為汽車零部件車間提供一套清晰的KBK智能起重機選型策略。
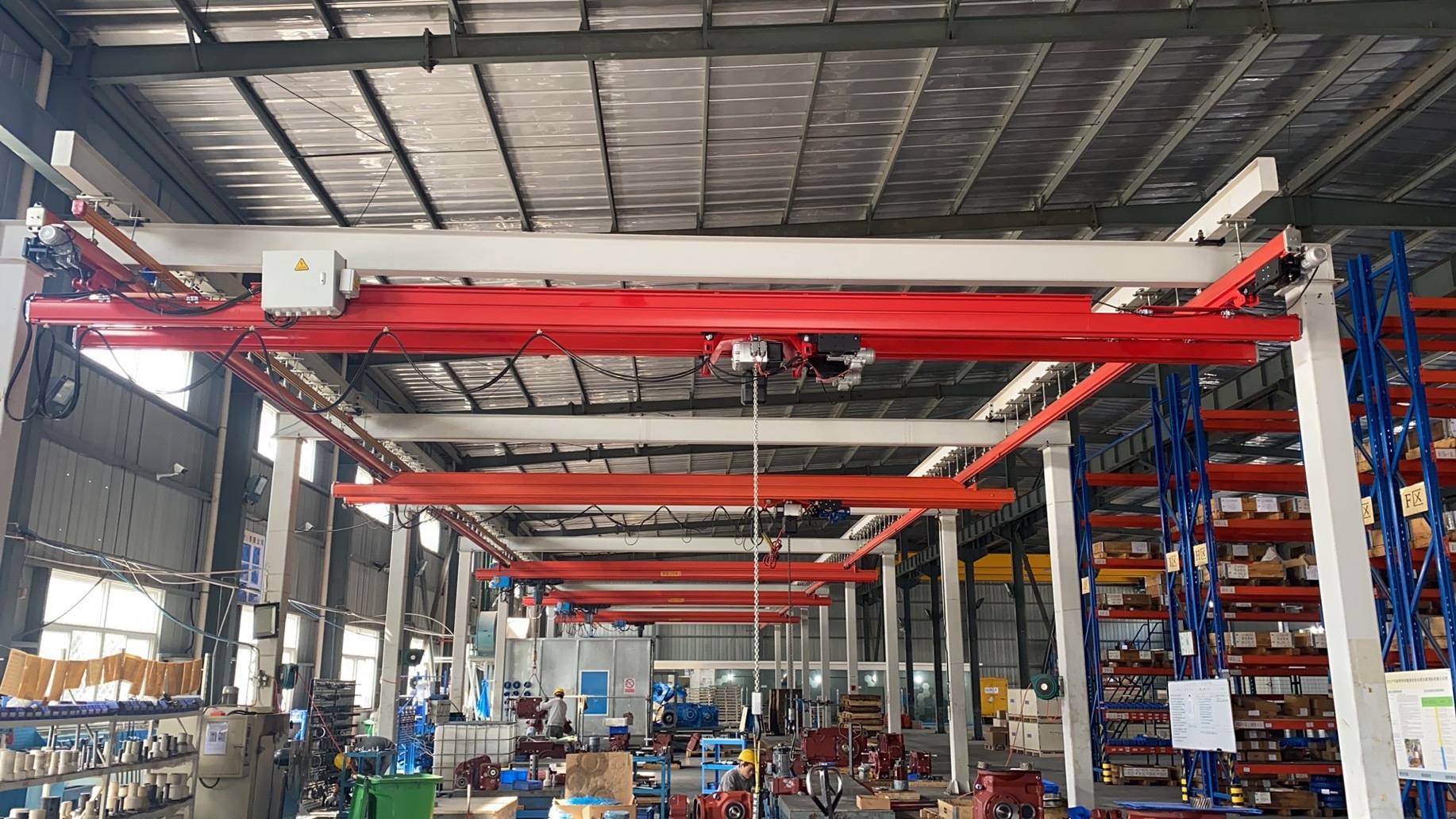
一、KBK起重機的核心優勢解析
1、空間利用率提升50%的模塊化設計
KBK起重機采用標準化軌道與組件,可自由組合為懸掛式或自立式結構。對于高度受限的車間,其無需立柱支撐的特點能最大限度釋放地面空間,尤其適合汽車零部件車間中設備密集的流水線布局。
2、毫米級精度滿足精密裝配需求
通過伺服電機驅動與智能防搖擺系統,KBK起重機可實現±1mm的定位精度。例如,在發動機缸體搬運或電子元件安裝場景中,精準的懸停功能可避免零件磕碰,降低廢品率。
3、柔性適配復雜生產節奏
支持手動、半自動、全自動多種操控模式,并能與AGV、機械臂聯動。當車間需要從“小批量多品種”轉向“大批量生產”時,只需調整程序參數即可快速切換任務,無需硬件改造。
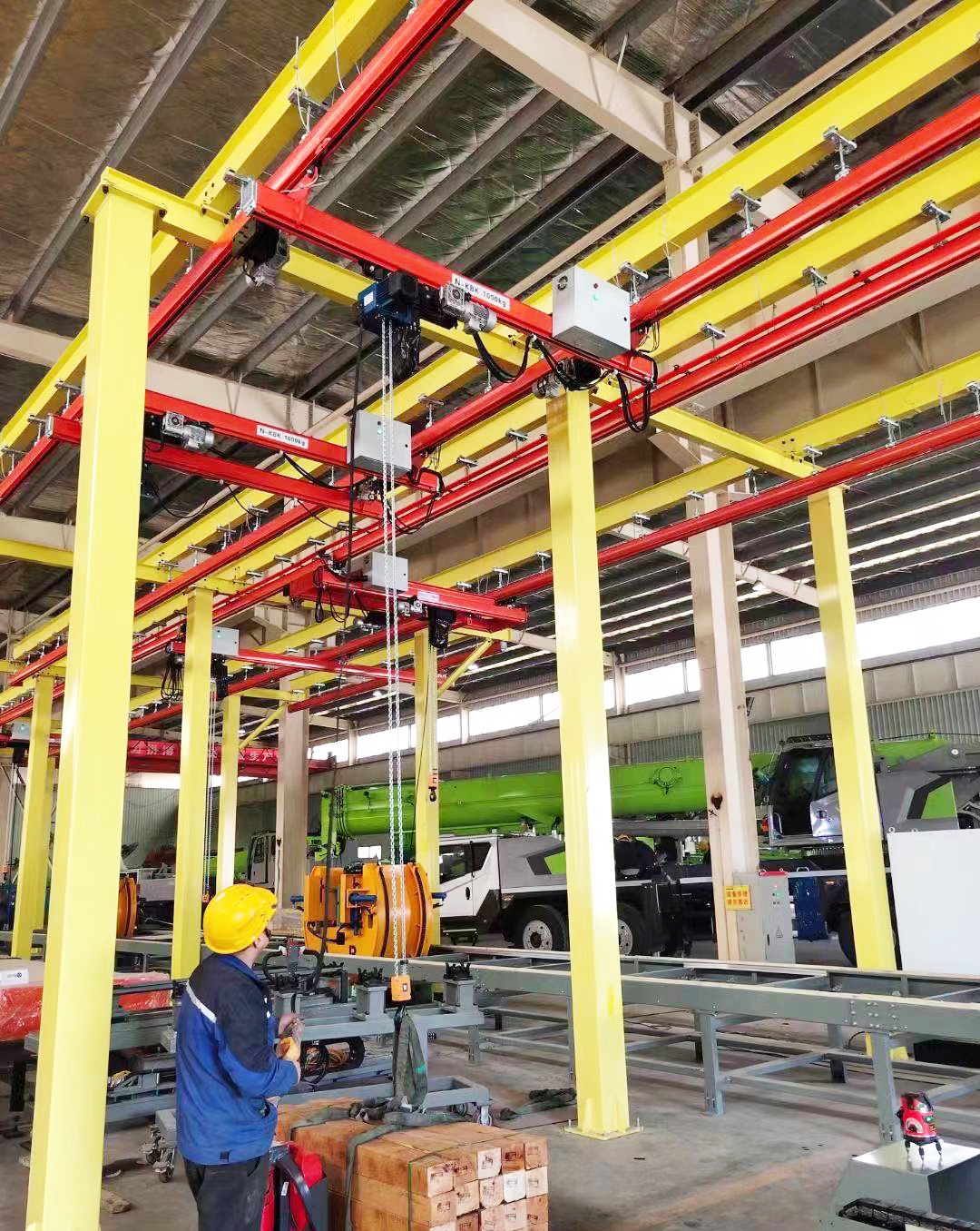
二、汽車零部件車間選型四大關鍵指標
1、載荷需求分級匹配
輕型搬運(0.5-2噸):適用于車門內飾、電子線束等組件,可選擇KBK-II型單梁起重機。
重型搬運(2-5噸):針對發動機總成、變速箱等部件,需配置KBK-III型雙梁結構并加裝安全制動裝置。
2、軌道布局與車間動線規劃
建議采用“主軌道+分支吊點”設計:主軌道沿生產線走向鋪設,分支吊點覆蓋工作站。例如,某新能源汽車車間采用環形軌道方案,使物料流轉效率提升30%。
3、智能控制系統選配原則
基礎場景:無線遙控器+機械限位裝置,適合預算有限的中小型車間。
高階場景:接入MES系統的物聯網模塊,實時記錄搬運數據并預警設備狀態,適合數字化工廠。
4、環境適應性強化設計
在焊接、涂裝等區域,需選用耐高溫(-20℃~150℃)型號,并增加防塵密封結構;潔凈車間則需符合ISOClass5標準的低顆粒物排放配置。
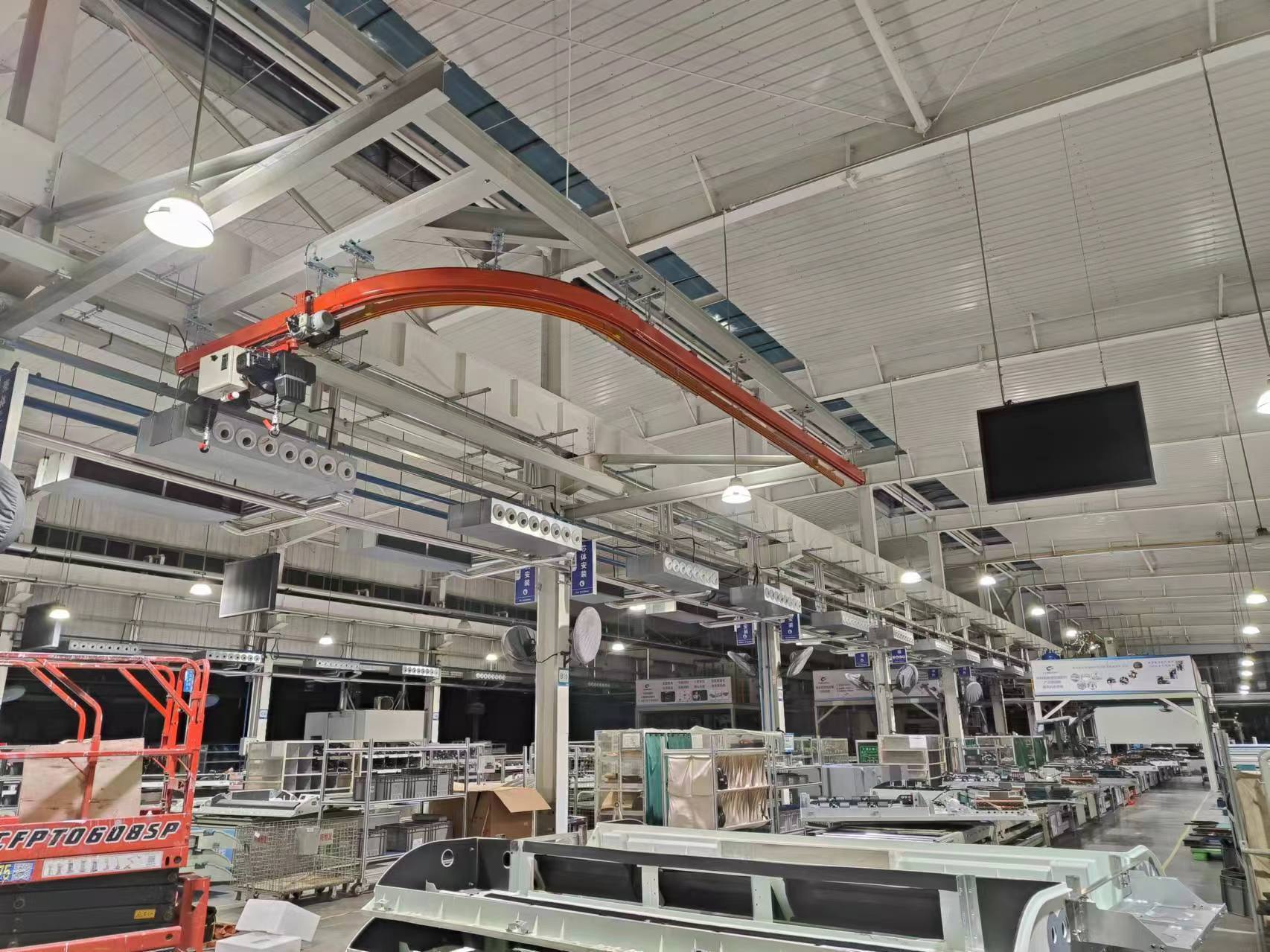
三、三步落地高效搬運方案
STEP1:需求診斷與模擬測試
通過3D建模軟件還原車間實景,模擬不同型號KBK起重機的運行軌跡,識別潛在干涉點(如通風管道、照明設備),提前優化布局。
STEP2:分階段實施策略
初期可在瓶頸工位試點單臺設備,驗證效率提升效果后再逐步擴展。例如,某零部件企業先為裝配線配備2臺智能KBK起重機,3個月內將工位切換時間從15分鐘縮短至4分鐘。
STEP3:持續優化與數據追蹤
利用設備管理平臺監測起重機使用率、故障率等指標,定期調整任務分配邏輯。數據顯示,合理保養的KBK系統可保持10年以上穩定運行周期。
選擇KBK智能起重機不僅是設備的更新,更是生產邏輯的升級。通過精準匹配載荷、空間與智能化需求,汽車零部件企業可構建柔性化搬運體系,為應對訂單波動、工藝迭代提供底層支持。建議企業聯合設備供應商開展深度診斷,用數據驅動決策,避免“過度配置”或“性能短板”的常見誤區。